Once your warehouse workers learn to pick and pack efficiently, you can improve the customer experience with on-time deliveries. Reliability and predictability have become expectations for consumers when it comes to purchasing. Here are ways to improve warehouse picking, which ultimately leads to better customer satisfaction.
Streamline Your Order Picking Methods
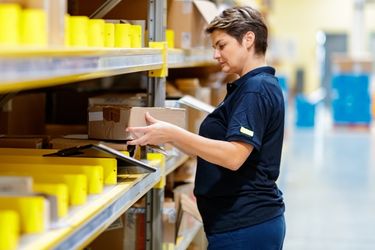
Picking in the warehouse world refers to when order pickers remove products from shelves and pack them for shipping to clients or customers. When a distribution center deals with high volume, it generates labor-intensive activity. But workers can become stressed or rushed by time constraints, leading to human error.
One of the ways to make warehouse picking more accurate includes simplifying storage strategies. It helps to separate products based on their demand. That way high-demand items are easier and faster to pick, while low-demand products can be stored in a different section out of the way. The duration of picking time should be a top concern for managers since it can slow down the shipping process.
A more advanced strategy is to invest in automated picking such as a conveyor with robot assistance. You still probably need a workforce, but automated pickers help speed up redundant tasks. Not only can machines handle picking, but they can also make use of machine learning technology to prioritize your picking list for maximum efficiency. Various picking techniques exist in the order picking process such as the following:
Batch picking: Combining multiple orders in small batches
Wave picking: Allocating a specific zone for picking multiple orders
Zone picking: Using a zone to pick one order at a time
Piece picking: Placing picked items in a container before shipping
Pick packing: Going through the warehouse to complete a picking list
Automated sorting system: A machine brings the item to the picker
The overall key to streamlining your business involves the synergism between the people you hire, the technology you purchase, and the procedures you implement.
Rethink Your Warehouse Layout
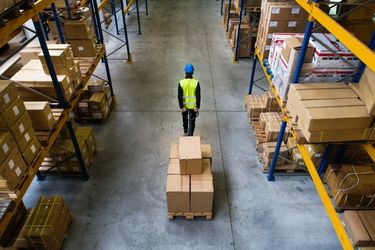
Warehouse picking productivity will rise dramatically by adjusting your layout. The key to warehouse layout optimization is for products to be loaded or unloaded in a safe and timely manner. A successful warehouse manager must be able to forecast demand accurately. Seasonal demand fluctuations might play a major role in your warehouse order picking, which may require routine layout adjustments.
Arranging your layout so that it matches your picking strategy is fundamental to establishing an effective process. Making sure high-demand products are easy to swiftly reach is a big step toward picking efficiency. A useful tip is to categorize products in three sections (A, B, and C) based on demand level.
Why Layout Matters
You can save storage space when you stack inventory items on pallets in an area designated for overflow. Pallets can be strategically used to maximize both horizontal and vertical space as long as items are easy to grab. Ideally, items are stored between knee and shoulder levels. By making items easy to remove, you will make picking a safer activity, which helps maintain business continuity.
Improving your layout will minimize errors, bottlenecks, and wasted time while accelerating picking speed. Ideally, your aisles are wide enough for allowing workers to easily transport items without bumping into anything. Clutter can lead to slowdowns, tripping, and injuries, so make sure walkways are clear.
Design A Warehouse Within A Warehouse
If you can group the top 20 percent of your products that account for 80 percent of orders, you maximize picking efficiency enormously. One way to do that is to build a warehouse within a warehouse. It reduces travel time and allows the picker to fill more orders at a faster pace. The manner in which you organize products can speed up picking time, such as organizing items by sales volume or stock-keeping unit (SKU), which is typically an 8-character code.
The more you isolate high-demand items from everything else, the more you'll control space and time efficiency. Slotting is the practice of grouping items together based on customized criteria that help make picking more convenient. One factor might be allocating items that require unpacking to specialists rather than regular pickers.
Learn From Your Picking Team
Keep your mind open to feedback you get from your picking team about what it would take to simplify the picking process. Your pickers might have better insights than supply chain experts about how to organize your warehouse layout. What works at one warehouse might not work at others, so find out what works best for your picking crew.
Consider strategically placing workstations in areas that eliminate wasted steps based on feedback from pickers. The less they need to move around, the more they can contribute to efficient order fulfillment. Your pickers might even have ideas on how to use pallets in ways that free up valuable space. As much as digital technology can improve your warehouse picking, you still need to make work comfortable for your staff.
Invest In Digital Technology
There are now plenty of ways in which a warehouse management system (WMS) can streamline your facility. Choosing the right software platform that fits your logistics operation and goals makes a big difference these days in gaining a competitive edge. Not only can a WMS empower a warehouse to organize inventory more efficiently, it gives you multiple ways to cut costs and save time. You'll enjoy more accurate picking and accounting as well as faster order fulfillment.
Investing in Industry 4.0 is essential for manufacturers of all types. Using IoT devices to monitor your production, storage and distribution will generate a wealth of information at your fingertips. RFID chips embedded in products are the key to tracking any item instantly in a vast warehouse with a barcode scanning device. This communications technology is particularly useful for automated picking.
One of your management goals should be to replace slow-moving inventory with a faster-moving inventory. You can move toward this direction by studying analytics generated by your WMS. The platform will give you real-time data on accurate stock counts and precise locations, as well as better forecasting to help you plan ahead. You can add various tools to your platform that helps you organize and prioritize your order mix.
Outsource Excess Order Flow
If your order flow starts to pick up beyond your ability to process orders in a timely manner, you can still capitalize on this growth by outsourcing excess orders to a third-party logistics (3PL) firm. The rise of 3PLs has correlated with the advent of smart technology. While manual picking can be the most time-consuming and labor-intensive aspect of order fulfillment, a modern 3PL can increase picking rates by as much as 60 to 100 percent.
Companies that aren't ready to invest in Industry 4.0 technology can still participate in this game-changing advancement by working with a 3PL partner that has adopted digital transformation. The most advanced 3PLs use automated picking equipment along with machine learning technology that helps accelerate order processing. Outsourcing logistics is a way to scale up your operations without changing your infrastructure.
Another advantage to outsourcing order fulfillment is that it can reduce the number of at-work accidents, which lead to downtime. In a third-party scenario, you store inventory at the 3PL's facility and they handle picking, packing, and delivery for your organization. A 3PL with advanced technology and real-time tracking tools can get products to customers quicker than traditional methods. Cutting down on time-consuming manual labor with a safer approach outside your facility reduces risks, which can lower insurance costs.
Aim For Customer Satisfaction
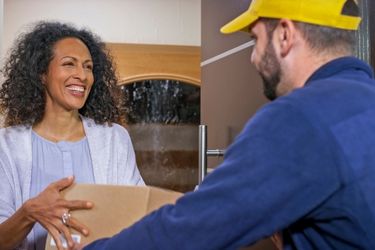
A crucial challenge to order fulfillment is exceeding customer expectations. When your warehouse experiences slowdowns, you need to assess the problem immediately, which can be done by studying real-time analytics. Packages that arrive early boost customer satisfaction, whereas packages that arrive later than expected can trigger suspicion, skepticism, and lack of loyalty.
Be aware that today's consumers consider on-time delivery to be a significant factor in whether or not they will order from the organization again. A recent survey found that 69 percent of retail consumers said they are less likely to buy from a retailer again if they did not receive ordered products within two days of the expected delivery date.
Shipping products to consumers on time relies on hiring competent warehousing specialists and optimizing the order picking process. That means training workers how to do their jobs efficiently is a major piece of the puzzle.
Conclusion
Making customer satisfaction your top priority will put your focus on ways to improve warehouse picking. With this clear goal in mind, you can maximize labor and technology to increase operational visibility and speed up warehousing processes. Another great place to start is making sure you have the right size pallets to help optimize your warehouse space.