Warehouses are the logistical backbone of the global economy. Although transport and retail play huge roles in moving products from manufacturers to customers, warehouse space is vital to store items and having them picked, packed, and shipped. In most cases, warehouses take advantage of vertical space, allowing more goods to be stored per square foot. Additionally, a warehouse management system (WMS) can be used to keep operations running smoothly by taking advantage of digital technologies for tracking packages as they arrive at and depart from warehouse facilities.
If you’re an operations manager at a large warehouse, you always look for solutions for improving warehouse productivity. Improved productivity can save time and make the packing and shipping processes more efficient. To help overwhelmed operations professionals get ahead of the curve, below are some tips for improving warehouse productivity:
Reevaluate Your Warehouse Layout
An efficient layout is one of the keys to running a successful warehouse operation. Just like how retailers rely on planograms to direct the flow of traffic in and around different sections of stores, warehouse work requires a similar approach. Warehouses are often designed to be outfitted to meet the needs of different suppliers, meaning there isn’t a one-size-fits-all warehouse layout. What works for one supplier may not work for another. You may need to reevaluate your warehouse layout and make changes to maximize efficiency.
You’ll also want to look at how goods are stored during your evaluation. Consider placing small items on higher racks and larger items on lower shelves. This reduces the potential for accidents and injuries. It may also make it easier to use pallets to move goods. Although pallets made from heat-treating wood are more durable than ever, anything you can do to reduce stress on pallets can be beneficial in the long term.
Utilize an Inventory Management System
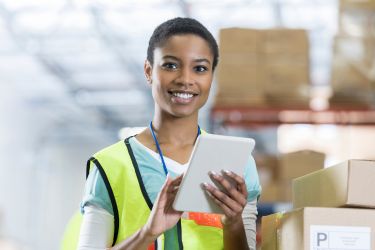
Another solution to improving warehouse productivity is utilizing an inventory management system. These are systems designed to track inventory levels and update them in real time as inventory changes throughout the day. As warehouse workers pick orders during their shifts, the inventory management system is updated when workers scan picked goods. This can improve warehouse efficiency by reducing the potential for out-of-stock items and delayed orders.
Modern inventory management systems can also use Internet-of-things (IoT) technologies. These are connected technologies that can interface with one another via the Internet and include everything from package intake scanning devices to the refrigerator in the warehouse break room. Because IoT devices can communicate with one another, they can pass along data about inventory. Smart devices can then use artificial intelligence and machine learning to adjust operations based on inventory conditions.
Survey Your Workers
As warehouse operations grow, it can be difficult for operations managers to find the time to visit the floor daily. You’re busy with so many tasks, and this may mean that there are productivity issues your workers see that you may have overlooked. If you’re trying to figure out how to improve warehouse productivity, consider surveying your workers on a semi-regular basis. A survey allows workers to provide feedback about what they see and deal with on the floor, allowing you to have a deeper understanding of potential bottlenecks that may hurt productivity.
As an added benefit, surveying your workers shows that you care about the opinions and experiences of your workforce. This can go a long way in building employee loyalty and helping retention efforts. Surveys also benefit your customers since increased efficiency and productivity usually means faster, more accurate service.
Work With a Safety Coordinator
Working with a safety coordinator can also improve your warehouse's operational efficiency. According to reporting by CNBC, some warehouse operations see workers injured at a rate of almost 7%. When workers are injured, they may miss work, so warehouse managers must act quickly to adjust schedules while managing normal operations. Additionally, injured workers often cost warehouse operations leading to lower operating capital.
Whether hired as a team member or brought in as a consultant, a safety coordinator can assess potential safety pitfalls. An action plan can be created to make the warehouse work environment safer. Sound safety policies can reduce accidents and injuries and make warehouses more productive.
Consider Your Pallets
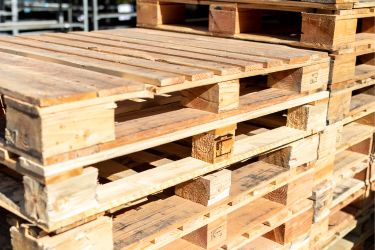
Pallets are essential to any warehouse operation, but using the right pallets can slow down your processes and prevent your warehouse from losing efficiency. These days, pallets can be made of wood and other materials, and recycled pallets are also available. Reconditioning existing pallets can save money, so consider whether your warehouse uses the right pallets for the goods it stores.
If your pallets aren’t getting the job done, working with a pallet manufacturer to find personalized solutions can help. A pallet manufacturer can assess your warehouse's and suppliers' unique needs to create a custom solution. When you have pallets matched to your equipment, processes tend to run smoother, lessening the chances for accidents, injuries, and damage to goods and packages.
Examine Last-Mile Delivery Options
In recent years, warehouse operations managers have been using last-mile delivery companies to great effect. These are logistics providers that handle mostly local deliveries. While some last-mile delivery companies work with suppliers, others are available to contract directly with warehouses. A last-mile delivery service generally picks up small loads or less-than-truckload (LTL) freight to be delivered directly to a buyer. Many use smaller commuter vehicles, including vans and pickup trucks.
The benefit to your warehouse is that goods can be organized to boost productivity. A section can be created for last-mile delivery pickups, allowing your warehouse to route goods more efficiently. This can also reduce congestion at loading docks, meaning larger loads move more efficiently.
Pay Attention to Consumer Trends
As was demonstrated during the Covid-19 pandemic, consumer trends can play a big part in shaping warehouse operations. Direct-to-consumer (DTC) became a trend during the pandemic, changing the way in which warehouses operated. While buying habits are moving back to retail as Covid-19 is largely in the rearview mirror, it’s still a good idea for warehouse operations managers to pay attention.
Failure to keep up with consumer trends may mean that your warehouse loses efficiency and wastes productivity. If buyer trends favor large amounts of smaller goods, your warehouse may need to reallocate space or reorganize its layout to adjust. Likewise, if large items are trending, new equipment may need to be purchased or existing equipment retooled in order to accommodate supplier and consumer demand.
Every Warehouse is Unique
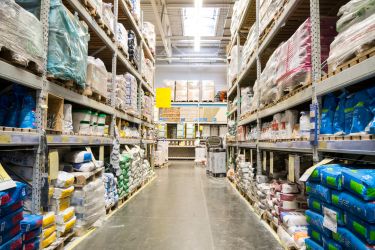
It’s also important to remember that every warehouse is unique. Geographic location, markets served, and demand for certain product categories can all have an impact on productivity and efficiency. This means that warehouse operations managers will need to take an individualized approach to meeting challenges.
For some, custom pallets may be the solution, but for others, a complete reworking of an operations manual or safety procedures may be in order. The key, however, is to document changes as they occur and analyze data regularly to determine what works and what needs to be adjusted to see a greater payoff.
Enhance Your Warehouse Productivity With the Right Pallet Partner
If you’re looking for more answers to the challenge of improving warehouse productivity, contact Pallet Market Inc. We’re among the leading pallet manufacturers in California, and our team is dedicated to providing the right pallet solutions to meet the needs of your warehouse operations.