If you have ever wondered how Amazon makes their warehouses hyper-efficient, continue reading. This article will examine Amazon's automation and data-driven approach to warehouse management.
Creating Efficiency Out Of Chaos
When one first looks at an Amazon warehouse, it appears to be nothing but chaos. There is no floor plan, no specific place for specific products, and products fly through the picking process at dizzying speeds without a great deal of human interaction. How did it get to this point?
Amazon has embraced the practice of random stowage since its early days in business. This is not a new concept, but it has increased in popularity over the past 25 years. It is estimated that at least 50 percent of warehouses also use this practice.
The Subtle Difference Between Business To Consumer (B2C) And Business To Business (B2B) Shipping
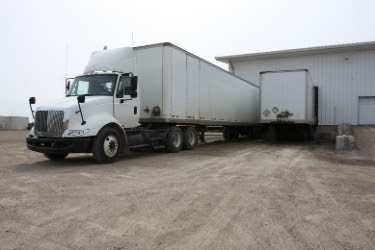
In a B2B model, boxes of products are shipped from one business to another business. Large offices order paper by the case, for example, rather than an individual ream. This results in the need to store large boxes of items in the warehouse.
Amazon's B2C business model allows it to stow items in the warehouse based on a straightforward principle. If there is space for it, that is where it goes. When shipping to consumers, they are more than likely ordering a single item rather than an entire box or pallet of items. This allows Amazon to split an incoming shipment into individual pieces and stow the products whenever it fits.
How Random Stowage Works
For example, if Amazon receives a box of 100 bars of soap, they store it individually as 100 bars of soap in as many as 100 different locations, rather than finding space for the entire box of bars. Their incredibly complex inventory management software keeps track of the areas of each bar of soap.
The Benefits Of Random Stowage
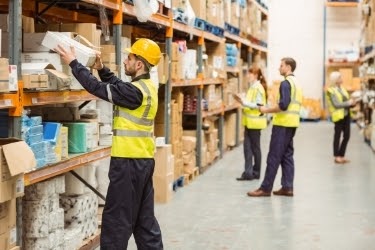
The primary benefit of random stowage is that it fills the warehouse much more efficiently from a space perspective. A fixed warehouse layout means that there must be space reserved for each product, creating unused space within the warehouse as shipments are stowed and then picked.
Considering that one of Amazon's warehouses can cover up to three football fields in size, that is already a tremendous amount of warehouse space. Multiply that by an ever-increasing number of fulfillment centers and hubs globally, and the amount of space is staggering. To utilize a traditional warehouse fixed floorplan when managing the shipment of 600 million different products would be impossible.
By randomly stowing individual items wherever there is space, there is no need to create space for the next box of incoming inventory. This allows the outgoing shipments to be picked from all over the warehouse, making an often unseen efficiency since there is probably one of the items close at hand to the selector, cutting down on wasted movement during the picking process.
Random stowage utilizes warehouse space more efficiently, reduces picking errors, and increases slotting and racking speed. This allows Amazon to optimizes its warehouses.
Economies Of Scale
The amount of merchandise stowed and shipped is immense. Amazon carries almost 600 million different products and ships up to 25,000 packages a day from each of its 145 global fulfillment centers. It is estimated that Amazon is responsible for 40% of online commerce. When you consider how many companies are in the online retail space, that is the reason that Amazon is the dominant player in this industry.
By driving the cost of fulfillment down, Amazon can offer consumers lower prices. Lower prices to consumers allow Amazon to sell more products, and more product volume results in even lower prices from manufacturers. This creates a climate of continuous growth for the company.
The Impacts Of Artificial Intelligence (AI)
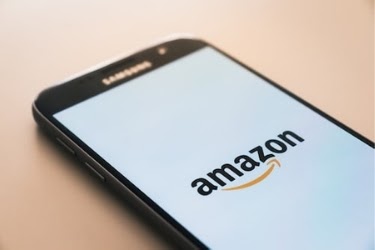
Amazon is dispassionately data-driven. Amazon's ever-improving algorithms meticulously analyze every bit of data collected from consumers. It has been said that Amazon will know what you want before you even know you want it in the future, and with its sophisticated marketing tools, Amazon's sales will continue to grow.
Random stowage cannot work at Amazon’s scale unless the algorithms controlling inventory management are continually tweaked and perfected to increase the warehouse's overall efficiency.
How Amazon Embraces AI
Amazon's algorithms that manage the warehouse and inventory control processes are continually being upgraded and improved. The data provided by its data collection and warehousing operation are also linked to its robotic workforce.
Amazon is also focused on linking big data to consumer behavior. Their advancements in speech recognition, which resulted in their Alexa family of devices, is another example of how the company is searching for ways to make buying easier for consumers.
The Amazon "Dash" buttons were another innovation that allowed consumers to press a button to have another shipment of a commonly-ordered product arrive on their doorstep, no computer required. To meet these consumer demands, Amazon is continuously looking for ways to improve its warehouse efficiency.
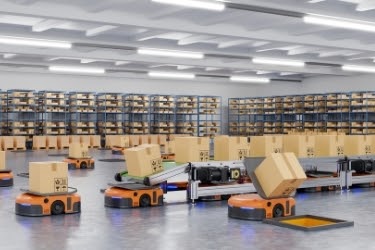
I, Robot
Amazon bought the company that manufactured its robots in 2012. It currently utilizes these robots in approximately 25 percent of its warehouses. Picking speeds have been improved by almost 500% in these facilities.
Amazon currently uses robots to move products from place to place and move entire shelves along a grid, taking the shelf to the selectors rather than the pickers to the shelves. As Amazon invests more money into robotics and converts more of its warehouses to this type of automation, its warehouse efficiency will continue to improve by leaps and bounds.
A Colossal Game Of Chutes And Ladders
When one enters an Amazon warehouse, the obvious first thing is a gigantic Escher-like mechanized game of chutes and ladders. Products move through the warehouse at blinding speeds through a series of conveyor belts and robotic shelving. The speeds that are achieved during the picking process would be impossible without this level of automation. Human beings cannot move that fast.
Always Looking To The Future
Amazon's research and development teams are continually looking for ways to improve efficiency and to work smarter. As their networks of warehouses and delivery hubs have grown, Amazon is now fighting to improve its "last mile" delivery service. They are experimenting with the idea of delivery by drone.
This push for speed comes from the desire to provide consumers with near-instant gratification. After all, if a customer can get their order in less time than it takes to get the kids dressed, drive to the store, stand in line at the checkout, and drive back home, it is a pretty compelling reason to order online.
Therefore, Amazon's goal is to improve its warehouses’ efficiency and the entire pack and ship process through delivery. This is evident when you examine how it has built its network of warehouses and fulfillment centers, including the advent of its "Prime Hubs."
The Human Element
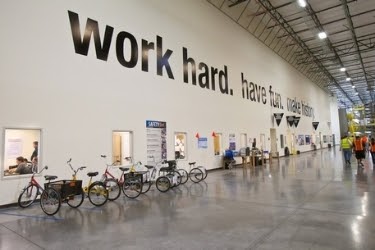
Workers are greeted by signs over Amazon's warehouses’ entrance with the slogan, "Work Hard. Have Fun. Make History." These six words are at the heart of Amazon's philosophy. For every disgruntled Amazon employee, there are others lined up to sing the company's praises.
Frankly, Amazon is doing as much as possible to eliminate the human element from its warehouse processes. Through artificial intelligence, robots, and warehouse automation, Amazon reduces the number of employees required to pack and ship merchandise worldwide. Automation leads to increased efficiency as humans are much more likely to make errors than an automated system is.
Does Amazon Merit Criticism?
The Internet is filled with vocal critics of Jeff Bezos' success, many citing the harsh working conditions in Amazon's warehouses. The company itself warns employees in their employment contracts that the job is stressful, and employees must agree to hold Amazon harmless from any stress-related impact the work has on their lives.
However, the fact remains that many of Amazon's managers and executives have been developed from within the company, rising from the ranks of temporary employees to overseeing large portions of Amazon's business. They are also considered one of the country's most diverse employers and have done a lot to support the LGBTQ community when other employers shun those with alternative lifestyles.
Critics point to terrible reviews on job sites like Indeed.com, where former workers complain about management pressure to improve productivity and performance continually. These negative reviews are not surprising given the sheer number of employees that Amazon hires and the fact that there will always be naysayers.
You Cannot Argue With Success
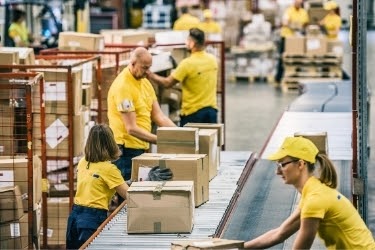
The seemingly disparate collection of warehouse processes and procedures are how Amazon makes its warehouses hyper-efficient. At first glance, their warehouses seem as if they are a random beehive of activity. Yet, a closer look reveals the genius of its automation and unrelenting pursuit of efficiency.
Whether you are a fan of Amazon's corporate culture or not, you cannot dispute that it has become a behemoth due to its ability to process and ship orders more efficiently than its competitors. It will continue to evolve and improve as time goes by because the soul of its methods embraces continuous process improvement. While one could argue that it is purely profit-motivated, that is the very definition of capitalism. Amazon's ledgers are undeniably bursting at the seams with profits.
If you are looking for custom pallets near you, take a look at solutions on this website. There are pallets for all kinds of businesses, from small, one-person warehouses to shipping behemoths like Amazon.