While there is a great deal of research on general warehouse best practices, many of those solutions do not apply to small warehouse efficiency. Often, small warehouses need more capital to execute frequently-suggested ideas such as automation, expensive software, or extensive infrastructure upgrades. From refining inventory management to perfecting warehouse layout, there are still several ways a small warehouse can become a powerhouse within the supply chain. Implementing these five strategies will improve your warehouse operations.
1. Increasing Inventory Accuracy
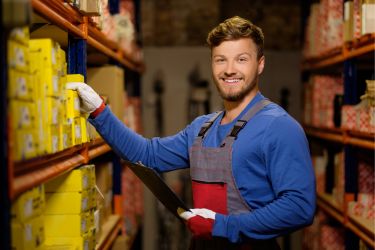
If your order fill rate is low and your inventory levels are high, your warehouse suffers from inventory mismanagement. Ensuring inventory accuracy is the first step in combating a low fill rate. Inaccuracy leads to wasted time, incomplete orders, back-ordered supplies, and customer frustration. Investing in warehouse management software that works with barcodes, QR codes, or RFID technology can cut down on inaccurate inventory levels. To grow customer satisfaction, choose cloud-based software that offers updates in real-time.
One of the best ways to ensure accuracy is to establish a continuous audit process like cycle counting. Instead of auditing all your inventory in a single monumental push every year, cycle counting means analyzing a small percentage of your items every day. Inserting an hour of cycle counting within your warehouse's daily schedule can significantly increase your inventory accuracy and amplify your order fill rate.
2. Managing Inventory Levels
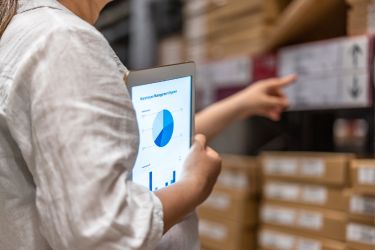
Storing low-demand items is expensive. If you are holding more than double the anticipated demand, liquidating the excess inventory might make more sense. Begin by closely scrutinizing items with the highest holding costs. Warehouse management systems (wms) can work with historical data to determine optimal reorder points. If your small warehouse cannot access past records, start keeping good records now so that next year's forecasting is more effective.
3. Improving Warehouse Layout
Often, labor is the largest variable warehouse operating cost. Because the highest percentage of labor is spent traveling from one area to another, layout plays a huge role in small warehouse efficiency. Because each operation is unique, there is no best way to organize a warehouse. However, adopting a velocity-driven layout will optimize your space. This strategy means locating your highest-demand items nearest the shipping area while your lower-demand items should be stored furthest from the shipping area. Another actionable way to improve your warehouse layout is to store items that are often ordered together within close proximity to each other.
4. Making the Most of Your Space
When it comes to small warehouse efficiency, storage management systems are just as important as warehouse layout. Narrow aisles make it possible to store more inventory without increasing costs. By expanding into unused vertical space, pallet racks allow for storing significantly more inventory without investing in a larger footprint. Of course, using the right pallets for your needs is another important piece in the pallet-rack puzzle. For example, understanding the difference between heat treated vs kiln dried pallets can boost your efficiency.
5. Optimizing Order Picking
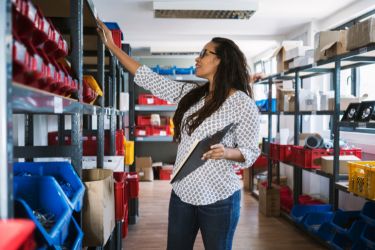
Travel time during order picking is generally the largest draw on your resources. If your warehouse experiences large orders, lots of time between orders, or your order picker capacity is small, picking a single order at a time might be the best strategy. However, in most other applications, batch-picking an order is more efficient.
There are two ways to approach order batching: via proximity and via time window. Which works better for your operation depends on the nature of your business. Batching via proximity means picking orders where different items are physically close to each other in the warehouse. Window batching entails picking multiple orders that arrive within the same time window. Order batching might lead to less distance traveled, but does mean that an additional sorting process is necessary.
Improving Small Warehouse Efficiency
To improve warehouse efficiency and productivity, focus first on reducing errors. This, in turn, will reduce costs. By prioritizing accuracy, reducing bloated inventory levels, reevaluating your layout, analyzing your space, and improving order picking, even a small warehouse can increase efficiency. To begin today, reach out to a contact in the pallet industry to find out what kinds of pallets are best suited for your operation.