Humans have been trying to automate manual processes since the invention of the water wheel. Over the decades, innovations in automation have led to some incredible breakthroughs for the logistics and manufacturing industries, and today’s digital systems have made it easier than ever to automate workflows. Automation can be one of the top reasons for outsourcing logistics tasks, but in-house automation solutions also provide benefits.

Warehouses in particular, along with the logistics professionals who serve them, have benefited from automation. The modern warehouse often contains automation technologies like robotics and computer-vision-assisted machinery. The various types of warehouse automation available in the digital age provide a range of benefits to both workers and customers, and many warehouses can be retrofitted with newer technologies to take advantage of automation without the need for a full tear-out and remodel.
If you’ve been considering adding automation to your warehouse or you’re curious to know whether your operations can benefit from automation, below are some of the leading reasons to consider warehouse automation technologies:
Consistent Accuracy Throughout Your Operations
Automating processes in a warehouse environment has been shown to not only improve accuracy but also to consistently improve accuracy. This means that fewer mistakes are made in order fulfillment, and accurate order fulfillment trends tend to remain on an upward trajectory when warehouse processes can be automated. This is not to suggest that your warehouse operations never experience mistakes when you automate or that you will never need to evaluate warehouse automation systems for accuracy, but it does highlight the fact that machines tend to be less prone to making the same mistakes over and over.
Warehouse automation can also improve efficiency in inventory control. By automating processes like order picking and packing, each process can be registered and tracked in real time. Your warehouse automation system might also have connection capabilities to connect to Internet of Things (IoT) devices for interfacing across your entire facility. As items are picked and packed, systems automatically update, providing both workers and your customers with insights regarding the progress of orders.
Labor Costs Can Be Greatly Reduced
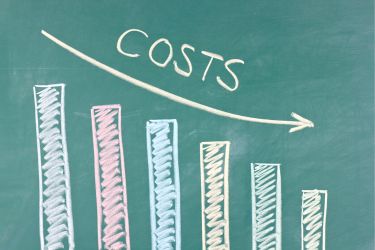
Warehouse automation can also reduce labor costs in many cases. As seasoned warehouse managers know, labor costs represent a large portion of warehouse expenses for most operations. Automation can reduce and even eliminate some of these costs by putting digital and robotic systems to work that don’t require time off, overtime pay or health insurance. Labor safety costs may also be reduced since warehouse managers don’t have to worry about injuries to autonomous mobile robots (AMRs) or automated storage and retrieval systems (AS RS).
Most warehouses also save money by upskilling existing employees to work in more advanced capacities in a warehouse that has implemented automation. Upskilling allows companies to make use of valuable employees who may not be able to fully contribute to warehouse operations in their current positions.
If an employee has been trained in order picking and an autonomous robot takes that worker’s place, the worker can then be trained to work with packing and shipping systems to monitor the progress of the autonomous mobile robot and evaluate warehouse automation systems instead. The machine handles the repetitive manual labor while the trained human worker takes on more complex tasks and contributes more to the warehouse overall.
Improved Supply Chain Efficiency
In any type of goods to person (GTP) operation, supply chain strength is vital. As was witnessed during the height of the Covid-19 pandemic, breakdowns in supply chains across the United States and the world practically ground many logistics operations to a halt. Automation helped save the day in many cases as logistics professionals scrambled to put all the pieces back in place.
Automation helps to keep supply chains running smoothly through networking communications. When a potential bottleneck is detected, automated systems can intelligently route elements to avoid disasters. On a smaller scale, automation systems can route pickers as they navigate pick to light and put to light systems, and automation connected to IoT systems can even take over the speed of conveyor system components as needed.
On the large-scale logistics side of things, updated information about the flow of goods and materials can be sent to centralized reporting systems. From there, software can make decisions about how best to route deliveries. These instructions are then sent to manufacturing facilities, pickup and delivery facilities and other links in a supply chain where autonomous robots can be made to behave accordingly.
Autonomous Warehouse Technology is the Future

As autonomous technologies have advanced in recent decades, it’s become clear that automation in logistics is here to stay. In fact, many consider the future of the logistics industry to be mostly autonomous in the coming years.
While there will almost certainly always be a need for human oversight to evaluate warehouse automation systems, many logistics companies and industrial operations are expected to benefit from automation as these technologies become more affordable and easy to integrate. Between the cost-savings, improved consistency and increased efficiency, now is the time to consider adding automation to your warehouse operations if you’ve been on the fence.
Learn More About Taking Your Logistics Operations to New Heights
Pallet Market, Inc. is your trusted source for warehouse and logistics solutions in pallet manufacturing and sourcing. Whether you’ve been searching the web for “custom pallets near me” or want to learn more about how warehouse automation can increase revenue, our team is here to help. Contact Pallet Market, Inc. today to schedule your discovery session with one of our industry experts! Call (909) 356-1263, or Schedule a Call to reach our team on the web.