When you improve warehouse quality control, you're doing a favor for the entire supply chain and fulfillment process. Supply chains are networks that require fast and clear communication about accurate information on supply and demand. Here are ways you can improve warehouse quality control, which will make your operation more competitive and favorable to everyone involved.
1. Tighten Up Quality Control Basics
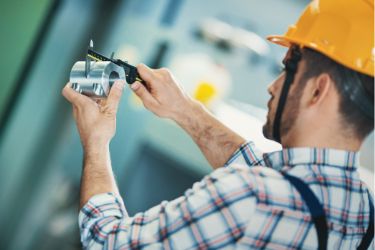
The first step to improving quality control is to understand why it exists, which is to limit errors such as wrong orders or defective products. Failure to see this last line of defense as critical is how a brand can swiftly alienate its customers and fall behind competitors. Here are seven basic tools for managers to use that can improve warehouse quality control:
- Cause-and-effect diagram - reveals the potential causes of a problem.
- These diagrams often originate from staff brainstorming sessions.
- Check sheet - allows employees to check off daily tasks. It can also be used for counting inventory and logging issues.
- Flowchart - displays a workflow in a step-by-step chart. This method allows a warehouse to improve with incremental changes.
- Control chart - shows how a workflow evolves. It presents lines for upper control limit and lower control limit, allowing you to compare these lines with current workflows.
- Histogram - reveals the frequency of a certain dataset. Managers can use histograms to analyze which problems occur the most.
- Pareto chart - this type of histogram comes from Italian economist Vilfredo Pareto and illustrates the distribution of issues. This chart helps managers prioritize the most significant problems to fix.
- Scatter diagram - shows the relationship between two variables. It gives managers insights on which variables to investigate further.
2. Inspect Individual Orders
To make sure order fulfillment is maximized, it's important for warehouse managers to assign warehouse quality control duties to experienced individuals with critical thinking skills. You should also be cognizant of the importance of hiring the right pickers and establishing warehouse picking best practices. The goal of reducing wasted inaccurate orders is a big part of achieving warehouse efficiency.
The more orders you have manually inspected by sharp quality control experts, the more you'll be able to identify the root of the problem that's causing inaccurate orders to flow through the system. It could be a new employee is making the same errors over and over.
It's important to understand from the beginning that you cannot just throw any employee into a quality control position. You need specialists with an eye for detail to do the job, otherwise, it can just lead to more inefficiencies. The more accurate order fulfillment becomes, the more you can reduce returns and raise customer satisfaction.
3. Invest in Streamlining Technology
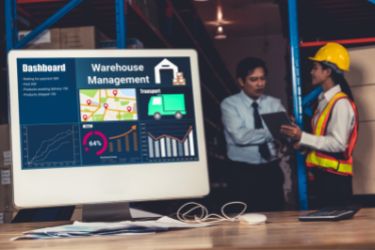
One of the most effective ways to improve your warehouse and customer satisfaction is to invest in state-of-the-art warehouse management software. Not only will it improve order accuracy, it lets you document problems easily, allowing you to move items such as defective products to specific locations. Your warehouse team will be able to locate products quickly with barcode scanners that connect with your infrastructure. Communication with the distribution center will be more seamless, as inventory management will be more simplified.
4. Track Your Daily Progress
Another excellent reason for a digital warehouse management system is to track your operational performance on a daily basis. Analyzing performance data will allow you to detect inefficiencies that need to be addressed immediately. It will let you know which team members are the most productive and do assignments in a timely manner with precision. It will allow you to analyze the shipping and receiving process, as well as improve storage strategies.
The key is to put the right people in place for positions that match their skills. Trying to make workers do things they don't understand is a huge waste of time unless you offer quality training. Many times this approach to management is the exact reason why the same mistakes keep piling up.
5. Make Quality Control a High Priority
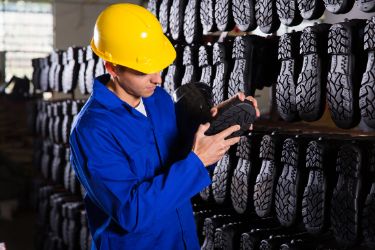
The best way to improve product distribution and inventory management is to make quality control an important aspect of your business. If you don't take quality control seriously, it's the same difference as letting things unravel and go to waste. Quality control is about analysis and communication - it's not a job for a newbie or someone who doesn't care about the company.
When you make quality control a top priority, your team will move toward an error-free operation, especially if you use AI software and automation. The result will be a stronger track record for on-time delivery and receiving, accurate documentation, and compliance with rules for loading and marking. Ultimately, you'll have fewer customer complaints and a better chance of boosting profit margins.
Conclusion
Study these methods to improve warehouse quality control. Once you've invested in high-quality warehouse management software, you need to hire and train the right people who understand the technology and logistics. Learn more about pallets for sale to make your warehouse even more organized.