The COVID-19 pandemic response created obstacles in the international and domestic transportation markets never before encountered. The challenges exposed significant risks in traditional freight management along the modern supply chain. As always, time means money. Now, companies face choices that go beyond conventional operational problems and less-than-truckload shipping.
The last mile service refers to the activities in the previous segment of the supply chain: delivery to the final destination. Technology solutions are providing greater visibility that goes beyond the supply chain management team. Delivery service is increasingly becoming part of a marketing strategy to build loyalty while promoting a competitive advantage.
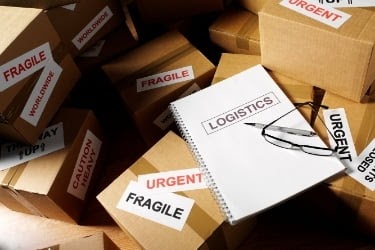
Failing to recognize the impact the pandemic has caused will lead to more problems. The solutions lie in adopting innovative technology to improve ROI and efficiencies from each supply chain resource. However, the last mile represents the most significant area of opportunity. Let’s take a look at how to solve the last mile problem in logistics.
Whether your company is analyzing the prospect of adding last-mile delivery services or seeking to improve existing services, you will want to address the potential pitfalls and challenges that come with managing this last leg of the journey.
Last Mile Challenges In Freight Management
While how to solve the last mile problem in logistics has always been a critical concern, it became even more critical due to the additional challenges caused by the pandemic crisis. More consumers shop from home, and e-commerce demand has burgeoned. The need for greater visibility into the final mile has grown as well. Consumers demand more knowledge in real-time. Where is the order? When will it arrive on the doorstep? Without this flow of data, your customers will likely switch to your competitor for future orders.
Also, the last mile problem includes ensuring driver safety. Companies are seeking to adjust, and some desirable services are in low demand currently. White glove services are an example.
What Makes The Last Mile So Challenging?
That last mile can be long. Without appropriate delivery infrastructure, journey time can be much longer than necessary. Routes are less efficient without the correct technology to plan them. Also, B2C deliveries are vastly different than B2B deliveries. Shipping is always a considerable cost. However, B2C shipping is typically less expensive, especially when bulk ordering items.
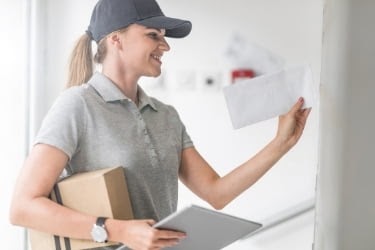
B2C deliveries have higher fuel costs and higher labor costs for relatively small, low-value shipments. Plus, consumers do not keep business hours. If a person is not home, the delivery driver may need to make multiple delivery attempts or drive to another location to drop the package for consumer pickup. Attempts may be further frustrated by remote areas, incorrect addresses, and order returns.
How do you reduce costs associated with the last mile? Below are several key ideas to achieve this objective.
4 Ways To Improve Last-Mile Efficiency
1. Efficient Proximity Between Customer And Warehouse
Rent is only one aspect to consider when deciding upon a warehouse. You must also weigh costs associated with delivery times and fuel usage. Your fulfillment centers and warehouses should be located to cover the most ground while being closer to consumers. At a minimum, most organizations keep west and an east warehouse for optimum delivery on either coast.
2. Improve Delivery Route Efficiency
Having well-planned routes can decrease delivery time and costs dramatically. Using the right software from a 3pl provider saves time over manually planning routes, and routes may be updated appropriately in real-time. It can also result in needing fewer drivers to make the same number of deliveries.
Delivery route planning software automatically accounts for location, time, traffic, and vehicle capacity to create the most efficient routes. Traffic updates can be sent directly to drivers in real-time, thereby empowering drivers and optimizing travel time.
3. Reduce Labor Costs By Adopting Auto-Dispatch
Auto-dispatch improves last-mile efficiency by decreasing the labor costs related to dispatch. The software enables your organization to assign deliveries to drivers automatically. It uses data on which drivers are active and their proximity to make the most efficient assignments. The technology may be integrated with delivery route planning to include the shortest route when the job is created.
Auto-dispatch provides many benefits. It balances assignments between multiple drivers, sets limits, and shows drivers as unavailable if they already have deliveries, even if that driver is closest to the delivery location.
4. Communicate With Customers
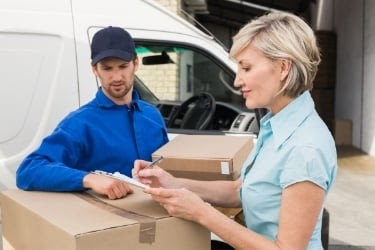
As noted above, consumers demand regular, real-time notifications at every point in the delivery process. They want to know every detail about their packages. This benefits the driver in addition to the consumer. The driver knows when the customer is available at the place and time of scheduled delivery. This technology enables your customers to track their package. Some software allows drivers to talk directly with customers and participate in the real-time feedback loop.
When the package is delivered, the driver can record proof of delivery, which documents and verifies that a package was left at the right door. It may include the recipient’s signature or a date- and time-stamped photo of the box on the porch. This helps your driver with proof if porch pirates strike, and it helps diminish fraudulent loss claims. With the right technology, drivers can complete the delivery process using a mobile app that supports collecting signatures, photos, notes, and barcodes.
If you are looking for the right source for pallets in California, consider our solutions at Pallet Market Inc. With decades of experience providing pallets for many business types from large, global enterprises to small mom-and-pop shops. Give us a call or fill out our Get a Quote form. We look forward to becoming a valuable resource for your business.