Manufacturers are turning to automated systems as a way to streamline warehousing. Robots can now be trusted to perform tasks more reliably and accurately than humans, which can help a producer reduce waste and losses in productivity. Not only can automation cut costs and save time, but it also speeds up picking and packing. Here's a look at how automated palletizing systems improve logistics.
Speeding Up Warehouse Processes with Automation
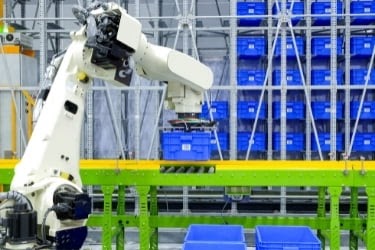
Palletizing is the system manufacturers engage in after a product has been made and is ready to be shipped. The traditional manual labor method is still used by many manufacturers today, while a growing number of robot-friendly companies are moving toward automation. The ability to stack a product without human labor helps cut costs. The heavier a product, the more efficient it is to have a robot rather than a human move it. Today's remotely controlled robots can be found on assembly lines.
Various automated palletizing systems exist to serve warehouses and other suppliers in the logistics field. Bastian Solutions offers two robot models for automated palletizing. Robotic palletizing is the more widely known and affordable model, while conventional palletizing encompasses bag and case palletizers and gantry crane palletizers. Meanwhile, Dematic makes user-friendly mechanical systems that emphasize cost-efficiency, flexibility, reliability, and high performance.
Today's fastest palletizer is FANUC's M-410iC/110, which gets up to 2200 cycles per hour. Another FANUC robot, M-410iB, can perform the work of four humans. This fast continuous 24/7 robot works well for a company that produces multiple product lines. Automated robots resolved many of last century's factory logistics vulnerabilities.
Steady Adoption of Robotic Warehousing
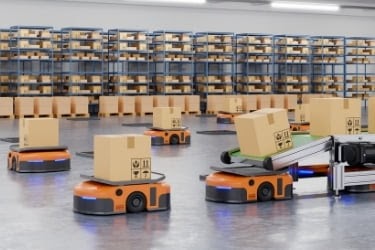
The growth of automated palletizing systems is spreading due to corporate giants like Amazon leading the way in using robots to improve warehouse efficiency. Learning about Amazon warehouse pallets can inspire warehouse managers to take a whole new approach to warehouse streamlining.
Amazon uses grid-based robots for transporting products from one location to another in a quarter of its warehouses. This modern automation has exponentially improved picking speed. While some critics worry that this model is replacing humans with robots, the technology is creating greater efficiency and accuracy for the company, generating greater output using fewer people.
Diversity of Palletizing Solutions
Various palletizing solutions using automation include robots that collaborate with humans. FANUC's CR Collaborate Robot Series is designed to replace machines that take up excessive floor space. These robots are programmed to stop when they come in contact with a human. Another emerging automation solution uses a 3D area sensor for decasing and depalletizing. Key benefits of these systems include optional full or partial automation, reduced warehouse labor costs, and precise sequencing of cases.
Centralized/mixed product palletizing helps sort 16 different product types from one line. An advanced robot used by Midwest Engineered Systems (MWES) includes vacuum grippers to handle and move products. The three main types of palletizing and depalletizing systems used by MWES are:
1. Inline palletizing - used for moving objects on mesh belt conveyors. This system maximizes the number of cases produced per hour.
2. Layer palletizing and depalletizing - designed for brands that offer a wide range of products with different requirements.
3. Mixed case palletizing - new packing solution for materials with various dimensions.
Specialized Robotic Functions
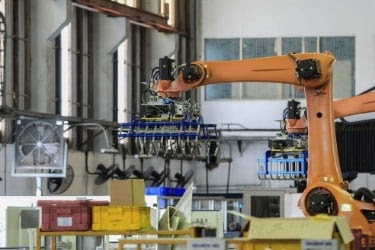
The types of robots an organization should choose to streamline its operation depend on the functions needed at the worksite. Different types of robotic arm tooling include clamps, a vacuum, and a fork style. The biggest question to ask should be about the kinds of products the robots will be handling. Another concern for tooling options is how fast the packaging line should advance in cases per minute.
The aesthetics of packaging should also be a factor for items being sent to retail or directly to consumers. That means selecting robots that do not degrade packaging with markings. Other questions to ask are: will robots be handling slip/tier sheets vs. pallets, and how will this system evolve in the future as packaging changes?
How Robotic Palletizing Beats Conventional Systems
Robotic palletizing is often favored over conventional palletizing in the current transformation to automation throughout the manufacturing and logistics industries because of its flexibility and adaptability for new products. Robotic systems can be used for low or high production volume. With the correct safety standards, any low-speed, simple case palletizing can be handled by the automatic palletizing process.
Simplifying multi-line case palletizing is achieved by using palletizing robots, again using low-speed operation. This system replaces sophisticated upstream accumulation conveyor systems. Clients may make changes to pallet designs with user-friendly graphics-based software.
Another technology for manufacturers and warehouses to consider is bag palletizing, in which a jointed-arm robot can palletize bags at over 20 cycles per minute. These robots can operate in confined or open areas. Pail palletizing involves robots stacking layers of pails on pallets based on programmed instructions. Warehouse stores use mixed, partial, or complex display loads for certain specialized situations. Overall robotic palletizing is the more cost-effective solution.
Conclusion
Investing in automated palletizing systems can make warehousing processes much more efficient, reducing labor costs. Since there is a wide range of automation systems available for warehousing, it's best to take a look at a list of options and narrow them down to fit company needs. Automation is the solution to greater productivity at a lower cost. Remember to prioritize what's practical over what's trendy. If you’re looking for used pallets for sale near me, contact Pallet Market today!