Although you may not realize it, maintaining warehouse inventory accuracy is more critical than you might think. Whether it is picking errors or wrong shipments, your company could be losing lots of money due to warehouse inventory mismanagement issues.
According to Multichannel Merchant’s research, each fulfillment error costs an average of $35 to $50. Fulfillment errors typically lead to higher return volume, negatively impacting the company's profit and increasing logistical issues. These errors will also increase customer service costs. These shipping errors also hurt customer satisfaction and loyalty. Overall, inaccurate warehouse inventory can be detrimental to your businesses.
Common Reasons For Inaccurate Warehouse Inventory
There are various reasons why companies have inaccurate warehouse inventory. Once you know the reasons for this, you can make the appropriate adjustments to improve warehouse inventory accuracy.
Here Are The Best Ways To Improve Warehouse Inventory Accuracy:
Competent Team Members On The Receiving Dock
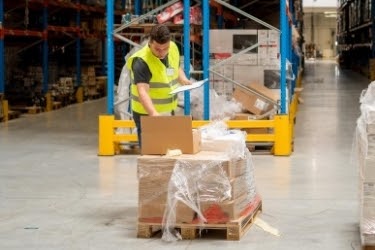
Having your best team members working in this area is the first defense for inventory accuracy. The members will visually inspect all inbound shipments, confirm that the right items and the right quantities are received, and compare these shipments and items to the packing slip and purchase order. They also can identify any damages.
A Good, Reliable Warehouse Management System
A warehouse management system will generate a license plate or a pallet identifier from an advanced shipping notice if inbound shipments are not already labeled for proper processing. You should then mark the inbound shipments, scan the identifiers of the high-quality pallets or the license plate, and confirm the quantities. Damages, shortages, or overages are communicated to customers so they will know immediately, they can inform suppliers, and order the final disposition for the receipt. Identifying any issues head-on will eliminate the impact of possible discrepancies toward the whole lifecycle for those items in the warehouse.
Utilizing Inventory Allocation Methods, Such As First-In-First-Out (FIFO) Or First Expiration First Out (FEFO)
You can eliminate the risk of waste, space usage, and more costs when your warehouse management system captures the warranty dates or shelf-life and allocates the inventory. You can then replenish accordingly as you forward-pick and according to the business rules and the customers' demand. If you follow this rule closely, there will be little to no obsolescence.
Maintaining Controlled Visibility
You should have a system that can visibly display where your inventory is located with the ability to zoom in or out in real-time. That way, you may trace an overlooked item that is recalled, reworked, etc.
Capturing All Possible Measurable Units For Outbound Orders And Inbound Receipts
Whether it is a case quantity or individual items, it is imperative to ensure you have the appropriate quantities and quantity sizes/measurements and the proper amount your company should have in the warehouse.
A Well-Organized Warehouse Layout
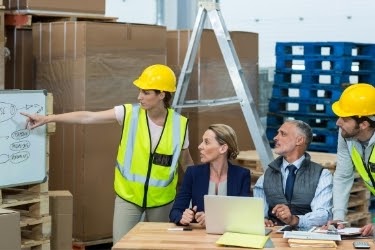
And while this seems to be self-explanatory, you may be surprised by how many companies are so wrapped in getting orders, that they significantly neglect to maintain a well-organized warehouse layout. Ensuring your warehouse is well-organized alone will save you money.
One way to ensure organization is by having outbound shipments and inbound receipts operating at separate doorways, so you won't mistakenly reship an order that is receiving inventory. Other tips to ensure organization include having different locations for forward pick and back stock, making time routinely for obsolescence and broken cases, not storing similar items or SKUs close together, clear labeling of all locations to avoid picking errors, and leveraging your directed picking solutions and warehouse management system.
With your top-notch picking solutions intact, workers can scan the wrong barcode, which will alert them that the incorrect item or location is selected. Also, there will be alerts showing the replenishment teams moving inventory from back stock to forward pick locations. There could be any movement detected or traceability by workers in case more training is required.
Communication
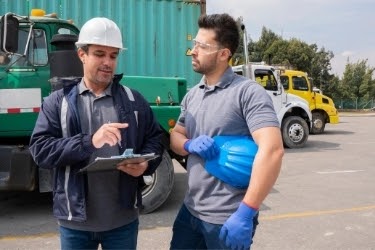
Another main factor includes maintaining a proper communication with a third-party fulfillment provider or with warehouse operations. Everyone involved can move accordingly upon getting advanced shipment notifications. Obtaining advanced notices about a change in suppliers for an item or getting a new thing introduced, for instance, will keep the operation running smoothly and efficiently without risking any adjustments or variances after receiving.
Conclusion
Improving warehouse inventory accuracy is much easier with the right software, a well-trained warehouse team, and a partnership with Pallet Market who offers a Drop Trailer Service.